Service
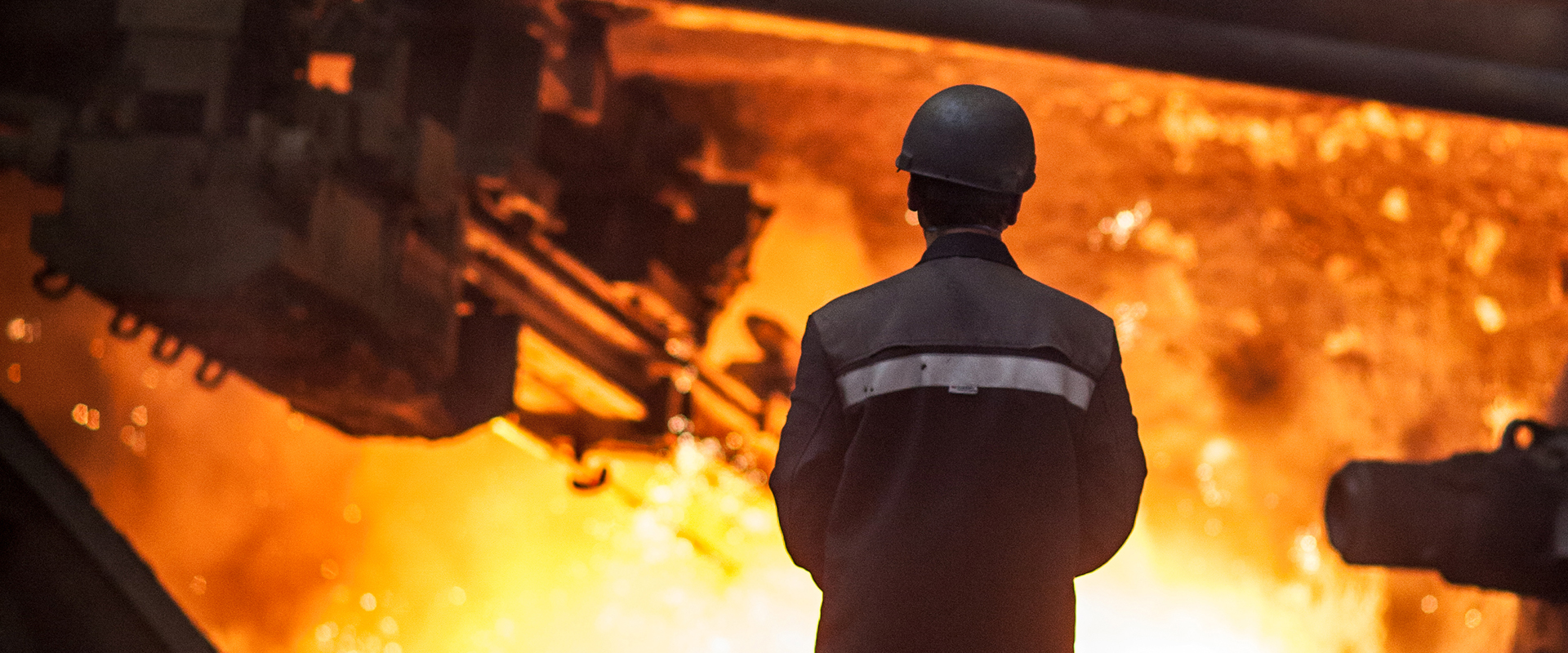
TMT Spare Parts
& Consumables
Always be on the safe side
The efficient and safe operation of a blast furnace requires reliable tapping machines and probes. OEM spare parts are crucial for the availability of critical furnace equipment, especially if your equipment ages. We can provide critical TMT spare parts with minimum lead time, e.g. in case of emergency.
Furthermore, TMT offers individual spare parts consulting services up to customer spare parts stock management assistance. TMT drill bars and bits are designed for optimum drilling performance under variable taphole conditions. In drilling tests, the best match of consumables for each installation is determined.
TMT consumables are continuously further developed in close collaboration with our customers. We validate the performance of every new TMT drill bit design as well as of every drill bar/bit combination on our drilling test stand.
Durability
Maximum equipment performance & longest lifetime
optimum safety of operation
State-of-the-art OEM spare parts & consumables
On demand
Long-term spare parts availability
Our product portfolio
TMT equipment and machines are designed to meet the specific requirements of blast furnaces. The high-quality, rugged design of all parts ensures long service lives and reliable functioning in daily operation, protecting your investment and ensuring high efficiency. Product improvements are continually incorporated into our products.
To maintain these benefits for you, we strongly recommend using original TMT spare parts.
Available in different dimensions and with any type of keyway
Many different types with and without carbide developed and available in any required dimension
Connection piece between machine and drill rod available in mutiple designs
The clay gun nozzle tips are always in contact with hot metal and slag during the plugging process. Therefore, the tips are subject to normal wear and need frequent replacement. TMT is offering wide range of nozzle tips according to latest design status.
The shields are protecting the equipment against heat and splashes and need regular replacement due to normal wear rate
TMT supplies various types of grate bars according to your material and design specification. Depending on your requirements we are offering you alternative manufacturing procedures such as lost-wax or sand casting method.
TMT hammer service
Perfect care
TMT-Group service centers provide TMT hammer refurbishments and repairs according to OEM standards all over the world. Our hammer service center network covers 6 continents: Europe, Asia, North America, South America, Africa and Australia/Oceania.
In a first step, trained specialists dismantle and analyse the hammer components in the service center. In a second step, an inspection report containing TMT’s repair and reuse recommendations will be issued to the customer for approval.
On top of that, customers generally receive operation and maintenance advice based on the wear pattern of their TMT hammers. TMT hammers that have been refurbished in a TMT Group service center furthermore benefit from a warranty on the repair scope.
Hammer refurbishment
Minimum replaced OEM parts during hammer refurbishment
Validation in advance
Customer validates repair scope before start of work
Warranty
OEM warranty on refurbished TMT hammers
TMT technical assistance
Expert support all over the world
TMT-Group offers a large service network to our customers with service bases all over the world. Our service product portfolio covers the complete lifecycle of TMT equipment.
Our vast design and service experience allows us to provide to the point technical assistance on TMT equipment. We cope with a large span of customer assistance requirements depending on our client’s maintenance philosophy and organisation including their individual repair schedules. TMT provides both local & remote technical assistance depending on the specific situation.
Expertice and
experience
High-level technical OEM competence paired with more than one century of experience
Always available
Large service network providing skilled service personnel all over the world. One dedicated TMT service center established in China and operational since 2012
Supported on
what you need
High flexibility of TMT assistance matching our customers’ demands
Changing organisation structures and personnel assignments are normal practice in many plants of our customers today. Long-term knowledge management for both operation and maintenance personnel can become challenging under these circumstances.
We offer TMT equipment inspections providing an in-depth evaluation of the current condition of tapping equipment and probes. A detailed inspection report informs our customers on recommended action points, both from a maintenance as well as from a spare part point of view.
Equipment inspections are ideal occasions to discuss available TMT equipment upgrades and new TMT software features. These inspections can easily be combined with operator or maintenance personnel training.
Inspections performed
by OEM specialists
High equipment reliability and minimum downtime
Safe equipment operation
and reduced operating costs
TMT recommendations on customers’ equipment operation and maintenance practice
Cost reduction
Combining equipment inspections with operator training
Consumables and spare parts always on stock
Get in Touch
Further information
If you have any requests, questions or needs, please don't hesitate to contact us. We will answer your inquiry as fast as possible.